The Basics of a Generator
A generator converts mechanical energy into electrical energy for running appliances in a power outage. It’s important to pick the right generator for your needs, and use it correctly to avoid fires or carbon monoxide poisoning.
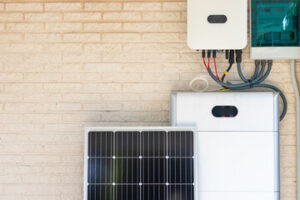
This portable generator runs on either gas or propane and can keep your lights on, refrigerator cold and sump pumps working in an emergency. It even has built-in carbon monoxide safety technology.
The engine, also called a motor in most cars, is the heart of your car’s power system. Its heavy lower section, the cylinder block, houses a number of pistons that pump inside it and connect to a crankshaft that turns them. The cylinder block has valve-controlled passages through which air and fuel enter the pistons, and others through which the gases produced by their combustion are expelled.
A four-stroke internal combustion engine, the most common in cars, works like this: The first “stroke” draws in air and fuel. The second stroke compresses the mixture. The third stroke ignites the fuel and combusts it. The fourth stroke pushes the resulting hot gases out of the cylinders.
Other engines don’t use fuel at all, but still exert mechanical work. They use other energy sources, such as nuclear fission in a steam or gas turbine to produce heat, which then powers the crankshaft of a gas or jet engine. In fact, the term engine is generally used to describe any device that converts other forms of energy into mechanical energy, including those that do it without combustion — like battering rams, catapults and artillery pieces.
The Battery
The generator’s battery provides the initial electrical power to start its engine. This is important because a generator’s starter motor requires a significant amount of electricity to turn over the internal combustion process that generates the generator’s energy. Generator batteries work much like batteries used in cars, cell phones and handheld games.
Inside a battery there are two pieces of metal in a liquid or paste-like electrolyte that transforms chemical energy into electric energy. The metals have points, called terminals, on each end that stick out of the battery. These terminals connect to an external circuit, allowing electrons to flow from the positive (-) terminal of one metal to the negative (+) terminal of the other. This electron tug-of-war between the anode and cathode forms conventional current, also known as electricity.
When the battery is connected to an electrical load, such as a light bulb, this continues the process. Light bulbs and other electrical devices use the resulting current to do work, such as turning the light on or off. The amount of work done depends on the type of electrical load and how long it is used. As the current flows through a wire and into a light bulb, it becomes hot. It is important to have a ventilation and cooling system that draws heat away from the generator’s various components.
Batteries can be arranged in several ways to increase their voltage, the amount of electric energy they can supply. They can be placed in parallel or in series. In a battery in series, the positive and negative terminals of each cell are connected to the anode and cathode of the next cell in the row. This increases the overall voltage but keeps the capacity the same.
Argonne is a world leader in battery research. Over the years, our pivotal discoveries have strengthened America’s battery manufacturing industry, aided in the transition of the U.S. automotive fleet to plug-in hybrid and electric vehicles and enabled greater use of renewable energy, including wind and solar power. Argonne’s research focuses on breakthrough fundamental science and technology, as well as accelerating the rate at which batteries can be recycled.
The Fuel Tank
A fuel tank is a safe storage solution for flammable liquids like diesel, gasoline and petrol. These tanks allow you to dispense the right quantity of fuel at the right time to keep your equipment in operation without having to make multiple trips. They can also help prevent leaking and spillage. The design and size of a fuel tank depends on the type of vehicle it is installed in. It is designed to seamlessly connect with generators, machinery and other devices that need a constant supply of fuel.
Often, fuel tanks have a built-in pump that creates pressure within the tank to push the fuel through pipelines or hoses toward its intended destination. They also contain a filter that removes impurities from the fuel. This prevents potential damage to the engine from contaminated fuel. Typical contaminants include dirt particles, water droplets and debris that may have entered the fuel during transportation and storage.
The tank also has a sending unit that monitors the level of fuel in the tank. The sender is connected to a variable resistor and float. When the float is near the top of the tank, it rests close to the ground, meaning that the wiper in the variable resistor is close to the ground and a small amount of current is sent back to the fuel gauge. As the float sinks, it increases the resistance in the variable resistor and sends less current to the fuel gauge.
Fuel tanks are usually made of metal or plastic (high-density polyethylene HDPE). While plastic is functionally viable for long periods of time, it has a tendency to absorb fuel vapors and degrade over time. If you have a plastic fuel tank, it is important to inspect it regularly for signs of damage or leakage and check that it has the correct insulation and shielding mechanisms in place.
Remote fuel tanks are essential to the proper functioning of any equipment that requires a continuous supply of fuel. They are also important in areas where access to a centralized fuel source may be limited. However, it is crucial to understand how a remote fuel tank works before using one in order to get the most out of your investment.
The Cooling System
A generator generates heat, and that heat must be removed to reduce the risk of damage to components. This is why the generator has a cooling system. Cooling systems can be air-cooled, liquid-cooled, or a combination of both. Air-cooled systems use a radiator that is mounted on or near the generator and forces ambient air over the core, which removes the generated heat. Liquid-cooled systems utilize a water pump and liquid coolant, usually a solution of antifreeze and water. These systems are more common in larger commercial and industrial generators.
Most cooling systems require routine maintenance and inspection. The manufacturer’s recommendations for these are important to follow. These should include checking for leaks in the radiator, fan, and oil cooler; inspecting the water pump weep hole; checking for signs of contamination in the cooling fluid (milky color or foam); checking the air filter; and looking for evidence of overheating.
The cooling system also needs to be engineered for the specific type and size of generator that will be using it. The cooling capacity required will depend on the work load that the generator will be expected to perform, as well as the temperature range. For example, the capacity of a vehicle radiator will need to be much greater than that of a smaller vehicle, as it will have to cool a larger engine.
In addition to the cooling system, a generator can be equipped with a heat exchanger to help remove thermal losses from the electrical conductors. The rotor windings are usually hydrogen-cooled, while the stator windings are made of hollow copper tubes that are cooled by water circulating through them.
Indirect cooling is used on large generators with power up to 60 MW, and this is the preferred method of cooling for most stationary applications. It provides a good balance between cost, reliability, and power handling capability. For generators that produce more than 1800 MW, the rotor is hydrogen-cooled and the stator windings are cooled by water. These large generators can also be cooled by using a water-to-air heat exchanger (TEWAC).